담배 제조기술 선도하는 KT&G - 900mg 한 개비에 담은 장인정신
담배 제조기술 선도하는 KT&G - 900mg 한 개비에 담은 장인정신
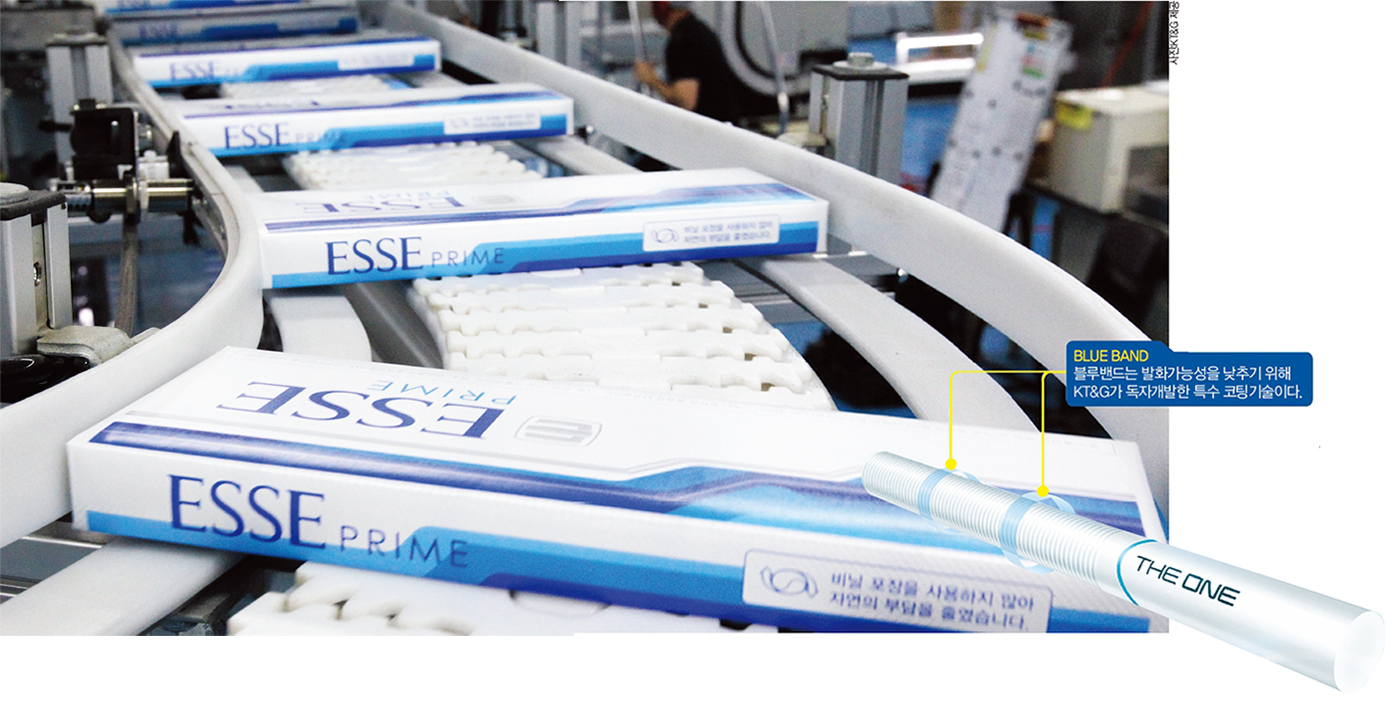
기술의 중요성은 담배산업과도 무관하지 않다. 간단해 보이는 담배 한 개비에도 수많은 기술이 들어간다. KT&G는 국내 고유의 담배 제조기술을 확보하는 데 주력하고 있다. 그 결과물 중 하나가 저발화성 담배다. 저발화성 담배란 일정조건 하에서 담뱃불이 쉽게 꺼지도록 만들어 화재의 위험성을 낮춘 제품이다.
담배사업법 개정에 따라 7월 22일 이후에 국내 담배 제조공장에서 출고되는 모든 제품은 저발화성 담배여야 한다. 하지만 기술의 진입장벽은 높다. 미국·캐나다·EU 등 일부 국가만 저발화성 담배를 도입하고 있다. 또 실효성 있는 기술 특허의 대부분은 전 세계 궐련지 공급 1위 회사인 A사가 보유하고 있었다. 그만큼 기술장벽이 높고 어려운 분야다.
어렵다고 포기할 수는 없었다. KT&G는 이미 5년 전부터 저발화성 담배 기술을 개발하기 위해 노력해왔다. 관련 제도의 법제화 논의가 있기 전인 2010년 일이다. 법과 상관없이 기업의 사회적 책임을 다하기 위해서라도 ‘저발화성 담배’를 개발할 필요를 느꼈던 것. 당시 제조분야의 직원들이 만든 사내동아리 ‘함박웃음’에서 최초 아이디어가 나왔다. 동아리 멤버였던 주성호 품질관리실 과장은 “세계적인 담배 회사도 저발화성 담배를 개발하다 어려워 포기했다”며 “사내에서 성공 가능성이 작고 제조원가가 상승할 수 있다는 우려의 목소리도 있었다”고 말했다.
글로벌 회사도 포기한 기술
KT&G는 개발한 기술에 ‘블루밴드’라는 이름을 지었다. 회사를 상징하는 색상인 ‘블루’로 명명한 것이다(실제 담배에 코팅된 밴드는 투명하다). 블루밴드는 고속으로 진행되는 담배 제조 공정 가운데 천연 특수물질을 궐련지에 코팅하는 기술이다. 미리 코팅한 궐련지를 공정에 투입하는 외국의 제조방식보다 한 단계 더 진화된 방법으로 평가된다. 현재 5건의 독자적인 특허도 보유하고 있다.
KT&G는 ‘더원’ 제품 3종에 처음 블루밴드를 도입한 이후 순차적으로 적용 제품을 늘려왔다. 법이 시행되는 7월 22일전에 선제적으로 모든 국내용 제품에 적용하게 되었다. 제품에 블루밴드를 적용하면서 발생하는 원가 증가분은 가격 인상 없이 내부적으로 흡수한다. 저발화성 담배를 제조하기 위해 일반 궐련지 보다 5배 가량 비싼 특수 궐련지를 수입할 수밖에 없었던 KT&G는 독자기술을 적용해 만들면서 연간 400억원 이상의 외화유출을 막을 수 있게 됐다.
KT&G가 담배 관련 기술을 통해 사회적 책임을 이행한 사례는 이번이 처음이 아니다. 2013년에는 궐련·필터 물리성 측정기인 ‘카디언’을 개발했다. 담배 한 개비의 무게와 둘레·길이를 세밀하게 측정하는 품질 측정장비다. 품질이 균일한 담배를 생산하기 위해서는 필수로 갖춰야 하는 장비였다. 이전까지는 외국계 대형회사로부터 장비를 조달해 사용하고 있었다. 장비 자체도 고가였고 유지·보수 비용까지 생각하면 막대한 국가의 부가 해외로 유출된 것이다. 이 사례는 중소기업과의 협업으로 더욱 빛을 발했다. 국내 중소업체인 ‘연백엔지니어링’과 함께 순수 국내 기술로 장비를 개발한 것이다. 2년이 넘는 연구·개발기간을 거쳤다. 현재 많은 국내외 필터 제작사들이 이 장비에 대한 구매의사를 밝히고 있다. KT&G는 필터 제조기 제작 회사인 ‘JK’의 제조기와 카디언을 하나의 세트로 구성해 해외시장에 판매하는 양해각서(MOU)를 JK와 체결했다. 카디언이 유럽의 메이저 3사가 독점하던 품질 측정장비 시장에 진출하게된 것. 측정장비의 최대 각축장으로 불리는 중국에서는 물리성 측정기 인증서도 획득했다. 이에 따라 소규모 내수시장에 머물던 ‘연백엔지니어링’도 글로벌 시장에 판로를 개척하는 효과를 거둘 수 있게 됐다.
KT&G는 기존보다 20% 낮은 가격에 품질을 측정하게 됐으니 진정한 의미의 상생이 이뤄진 셈이다.
국내 중소기업의 수출길 열어
담배 한 개비의 평균 무게는 900mg이다. 이 작은 제품 속에 기술 개발을 위한 치열한 땀과 노력, 그리고 중소기업과의 상생이 녹아 들어가 있다.
ⓒ이코노미스트(https://economist.co.kr) '내일을 위한 경제뉴스 이코노미스트' 무단 전재 및 재배포 금지
많이 본 뉴스
1가수 우즈 측, 故 김새론 열애설에 “아티스트 사생활…확인 어려워”
2‘위증교사’ 재판받던 전북교육감 처남, 차 안서 숨진 채 발견
3민주, '당원투표 50%·국민여론조사 50%'로 대선 후보 선출
4광명 붕괴사고 하루 경과…실종자 수색작업 총력
5더불어민주당 “尹, 개선장군 행세하며 '퇴거쇼'…퇴근시간 퍼레이드 민폐”
6안철수, 오세훈 불출마에 “마음이 숙연…당 재건 위해 큰 역할 해주길”
7넥써쓰, 중국 이어 두바이까지…해외 진출 본격화
8오세훈 서울시장, 대선 불출마…“비정상의 정상화 위해 백의종군”
9위믹스 생태계 구축으로 국내 블록체인 시장 선도한 위메이드