포스코, ‘e Autopos’로 친환경 뉴모빌리티 소재산업 선도
최첨단 철강소재 적용으로 친환경차 미래 제시
외부 충격 흡수하는 포스코 첨단 강종 다수 포함
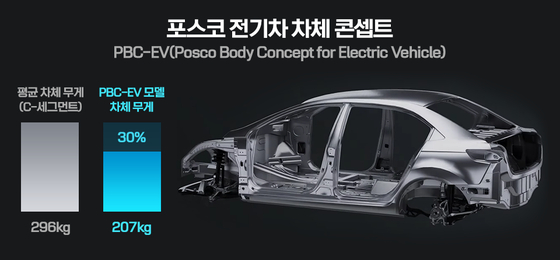
창립 53주년을 맞은 포스코그룹이 그린(Green·친환경)과 모빌리티(Mobility·이동수단) 중심으로 사업구조를 바꾼다. 전기차 강재 및 부품, 이차전지소재, 수소 등 친환경 사업이 주축이다.
최정우 포스코 회장은 지난 4월 1일 임직원들에게 보낸 메시지를 통해 “저탄소·친환경으로 대변되는 메가트렌드 전환 국면에서 포스코그룹은 전기차 강재 및 부품, 이차전지 소재, 수소 등 친환경 사업을 선도해야 한다”고 밝혔다.
그는 이어 “그룹 역량을 결집해 리튬, 니켈, 흑연 등 원료부터 양·음극재로 이어지는 밸류체인을 강화하고, 전기차 시장의 신뢰 받는 공급자, 파트너로 성장하자”고 강조했다.
친환경 차체·샤시용 고장력 강판 개발
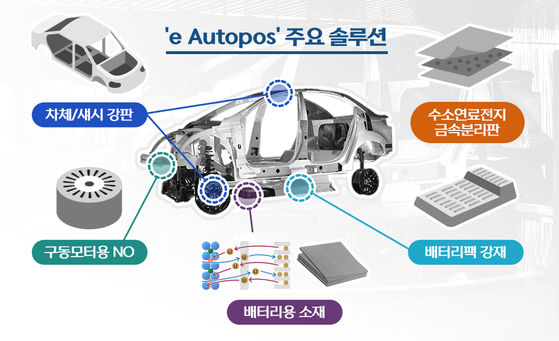
포스코는 올해 초 친환경차 시장을 선도하겠다는 목표를 내걸고 친환경차 제품·솔루션 통합 브랜드인 ‘e Autopos’를 론칭했다.
e Autopos는 친환경의 ‘eco-friendly’, 전동화 솔루션의 ‘electrified AUTOmotive solution of POSco’를 결합한 합성어다. 친환경성·협업 시너지·미래지향을 담은 혁신으로 친환경차 시장을 선도하겠다는 포스코의 의지가 담겨있다.
브랜드의 주요 제품으로는 차체·샤시용 고장력 강판, 배터리팩 전용강재, 전기차 핵심부품인 구동모터의 고효율 하이퍼(Hyper) NO 전기강판, 수소차 연료전지 금속분리판의 Poss470FC 스테인리스강판, 이차전지소재용 양·음극재 등이 있다.
e Autopos 제품이 적용된 차체는 가벼우면서도 강하다. 환경을 지키기 위해선 자동차를 가볍게 만들어야 한다. 전기차는 배터리팩 무게로 인해 내연기관 차량 대비 200㎏가량 더 무겁기 때문에 전기차에 있어 ‘경량화’는 필수 과제다.
이에 포스코는 ‘기가스틸’을 사용한 포스코 고유 전기차 차체 솔루션인 PBC-EV(Posco Body Concept for Electric Vehicle)를 개발했다. PBC-EV는 기가스틸을 45% 이상 적용해 기존 동일 크기의 내연기관 차량 대비 약 30%의 경량화를 달성했다. 기가스틸은 최근 자동차 차체 적용이 증가하고 있는 알루미늄보다 3배 이상 강하며, 1㎟ 면적 당 100㎏ 이상의 무게를 견딜 수 있다.
e Autopos 차체 솔루션에는 포스코의 첨단 강종이 다수 포함돼 있다. 외부 충격 시 승객 및 배터리 공간은 변형되지 않도록 설계해야 하고, 구동모터·트렁크 공간은 물론 측면 공간 또한 충분한 충돌 에너지를 흡수하도록 설계돼야 하기 때문이다.
이와 함께 포스코는 자동차의 기본인 주행기능을 담당하는 ‘섀시’ 에서도 e Autopos 솔루션을 제공한다. 차체의 바닥부에 연결된 섀시의 역할은 크게 주행과 충격 흡수 두 가지이며, 섀시는 차량이 달리는 데 필요한 최소한의 기계 장치인 현가장치(Suspension), 허브베어링(Hub Bearing) 그리고 노면의 충격을 흡수하는 현가스프링(Suspension Spring), 쇼크업소버(Shock Absorber) 등으로 구성된다.
현가장차에도 포스코는 여러 강재들을 적용해 더 가볍고, 더 오래 사용할 수 있는 부품들을 개발했다. 자동차 휠에 장착되어 바퀴가 회전하도록 도와주는 허브 베어링에는 포스코의 베어링강이 쓰인다. 포스코 베어링강은 탑승자의 안전과 직결되는 바퀴에 사용되는 부품이기 때문에 가장 엄격하게 품질이 관리되며 마모, 균열, 변형에 강하다는 특징이 있다.
e Autopos의 솔루션이 적용된 타이어에는 포스코 타이어코드 선재가 적용돼 있어 펑크를 최소화 한다. 또한 타이어코드는 차량의 무게를 지탱하고 타이어 모양을 유지할 뿐 아니라 타이어 수명을 늘여주는 강선으로 포스코의 타이어코드 선재는 고강도탄소로 가공성이 우수하고 강도가 높아 경량화 및 주행 안정성이 탁월하다.
노면에서 전달되는 충격이나 떨림을 최소화해 편안한 승차감을 책임지는 현가스프링에는 포스코의 스프링강이, 쇼크업소버에는 포스코의 기계구조용 탄소강이 적용된다. 특히 포스코 스프링강은 일반적인 스프링강보다 강도가 200MPa 이상 높으면서도, 스프링 강선이 감긴 횟수가 적어 15%가량 가벼워 경량화에 제격이다.
전기차 구동모터 위한 특별 소재 개발
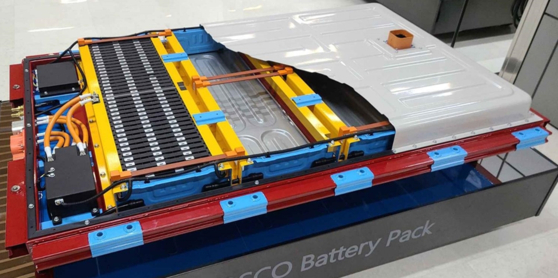
포스코는 무방향성 전기강판인 하이퍼 NO를 적용한 구동모터도 개발했다. 모터는 전기차의 연비를 향상시키는 핵심 부품으로 전력 손실이 낮은 전기강판이 필요한데, 포스코는 하이퍼 NO 적용으로 기존의 전기강판 대비 에너지 손실을 30% 이상 낮췄다.
여기에 포스코는 접착제 역할을 하는 코팅을 전기강판 표면에 적용하는 ‘셀프본딩’ 기술도 더했다. 셀프본딩을 활용하면 용접 등 물리적 방식과 달리 전기강판의 전자기적 특성을 저하시키지 않아 모터효율을 향상시킬 수 있다. 기존 용접체결 방식보다 모터코어의 에너지 손실이 10%이상 낮은 것으로 조사됐다.
포스코는 글로벌 완성차사와 부품사에 전기강판 및 이용 솔루션을 직접 제공하는 등 네트워크 강화를 통해 판매를 확대중이다. 특히 포스코SPS는 전기강판으로 구동모터코아를 생산해 부가가치를 높이고 있으며, 포스코인터내셔널도 국내외 판로 확대에 힘을 보태고 있다.
이외에도 포스코는 기가스틸과 스테인리스강, 그리고 선재를 사용해 3세대 전기차 스케이트보드 구조에 대응하는 e Autopos의 친환경차 배터리팩 PBP-EV(POSCO Battery Pack-Electric Vehicle) 개발을 완료했다. PBP-EV는 여러 개의 모듈(Module)에 각종 제어 및 보호 시스템을 장착한 부품으로 포스코 고강도 강판과 기가스틸이 적용됐다. 이를 통해 배터리팩 안정성은 물론 경량화에도 성공했다.
배터리팩에 쓰인 스테인리스강은 자동차의 외부 충격, 열, 진동 등으로부터 보호하기 위해 배터리셀들을 일정 개수로 묶은 모듈의 외곽 프레임 구조에 적용된다. 스테인리스강은 강도가 높고 부식에 강하기 때문에 배터리 충‧방전중 배터리셀의 부풀어오름(Swelling)을 억제하고, 배터리팩 내부 습기에도 녹슬지 않는 장점을 가진다.
e Autopos의 배터리팩의 기본 구조는 롤포밍 폐단면 프레임 타입으로 배터리 용량이 60kWh, 배터리팩 총 중량 424kg, 케이스 무게는 73.8kg다. 기가급 이상의 철강재 Mart1470, CP1180, 980DP를 적용해 초경량의 무게로 설계됐고, 제작 원가는 동일 용량의 알루미늄 배터리팩 케이스 대비 70% 수준으로 절감 가능하다.
한편, 포스코는 전기차 배터리 등 이차전지 소재사업도 경쟁력을 강화하고 있다. 포스코그룹은 전 세계에서 유일하게 리튬, 니켈, 흑연 등 원료부터 양극재와 음극재까지 이차전지 핵심 소재관련 일괄공급체제를 갖췄다. 이를 기반으로 2030년까지 양극재 40만톤, 음극재 26만톤 생산체제를 구축해 이차전지소재 부문에서 글로벌 시장 점유율 20%, 연매출 23조원을 달성할 계획이다.
포스코케미칼은 차세대 양극재, 음극재 개발에도 매진하고 있다. 양극재는 전기차의 주행거리에, 음극재는 배터리 수명과 충전시간에 영향을 미친다. 포스코케미칼은 ‘1회 충전시 주행거리 600㎞’를 목표로 에너지 밀도를 높이는 High니켈 기반의 양극재를 연구하고 있다. 또 ‘10분 급속충전’을 위해 구조안정성이 높고 팽창성이 낮은 인조흑연 음극재도 개발하고 있다.
차완용 기자 cha.wanyong@joongang.co.kr
ⓒ이코노미스트(https://economist.co.kr) '내일을 위한 경제뉴스 이코노미스트' 무단 전재 및 재배포 금지
많이 본 뉴스
1한투운용 ACE 인도컨슈머파워액티브, 순자산액 500억원 돌파
2교보증권, STO사업 위한 교보DTS·람다256 MOU 체결
3"누나는 네가 보여달래서…" 연애한 줄 알았는데 잠적?
4‘이것’만 있으면 나도 백종원...팔도 왕라면스프, 누적 판매 300만개 돌파
5중견기업 76% "트럼프 2기, 한국경제 불확실성 높일 것"
6'비트코인 큰 손' 마이크로스트래티지, 5만5500개 추가 매수
7"오! 야망있네~" 김종민 연하女와 결혼? 역술인 말하길…
8평양간 백지영, 예정에도 없던…北에서 기싸움도?
9신세계免, 인천공항 T2에 체험형 쇼핑공간 ‘신세계 존’ 완성