아반떼 이렇게 만들었구나...尹 대통령도 반한 세계 최대 규모 공장[가봤어요]
세계 최대 규모 단일공장 ‘현대차 울산공장’
아반떼·베뉴 만드는 3공장, 의장라인 돌아보니
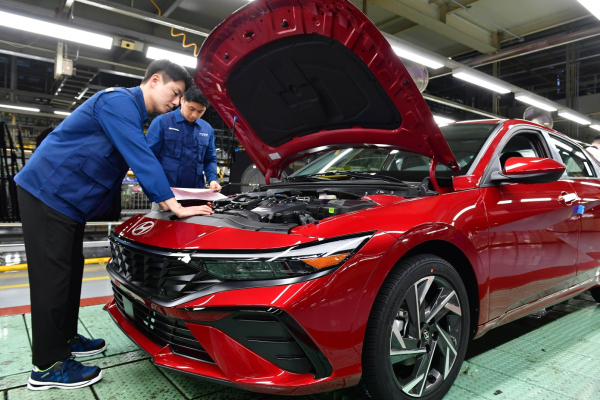
[이코노미스트 이지완 기자] “사진 촬영, 녹음 등은 절대 불가능합니다.”
10월 18일 오후 4시 방문한 현대자동차 울산공장. 국내 대표 자동차 제조사인 현대차의 핵심 기지답게 보안 규정은 매우 엄격했다.
버스를 타고 목적지인 울산 3공장으로 이동하는 10분여 정도의 시간 동안 창문 너머로 제네시스 GV80, G80, 아반떼, 코나, 베뉴 등 수많은 차량이 눈에 들어왔다. 태어나서 이렇게 많은 차를 동시에 본 것은 처음이었다.
1967년 설립된 현대차 울산공장의 부지는 여의도 전체면적(840만㎡)의 3분의 2에 달하는 약 500만㎡(약 150만평) 수준이다. 이곳에 5개의 독립된 공장설비(울산 1~5공장)가 자리잡고 있다. 현대차 울산공장 관계자는 “단일 자동차 공장으로는 세계 최대 규모”라고 설명했다.
워낙 규모가 커 걸어서는 이동이 불가능하다. 현대차는 직원들의 원활한 이동을 위해 공장 내에서만 21대의 구내버스를 운행하고 있다. 버스 정류장의 수는 44개에 달한다.
울산공장은 현대차의 핵심 생산시설이다. 총 3만2000여 명의 임직원이 9.6초당 1대, 하루 평균 6000대의 차량을 생산한다. 연간 생산 가능한 대수는 총 140만대에 이른다. 지난 3월 윤석열 대통령이 방문해 화제가 되기도 했다. 당시 윤 대통령은 정의선 현대차그룹 회장과 함께 생산라인, 수출선적부두 등을 돌아봤다.
이날 둘러본 울산 3공장은 우리에게 친숙한 아반떼, 베뉴, i30, 코나 등을 생산하는 곳이다. 3공장은 일반인들에게도 열려있는 곳이다. 현대차 홈페이지에서 견학 신청을 하면 투어가 가능하다고 현대차 울산공장 관계자는 귀띔했다. 이 관계자는 천장을 따라 걸으며 위에서 아래를 내려다 볼 수 있는 별도의 길이 만들어져 있어 직원들의 작업에 방해가 되지 않는다고도 설명했다.
울산 3공장 내에서도 의장라인을 중점적으로 둘러봤다. 의장라인은 차량의 핵심 부품 등을 조립해 차를 완성하는 마지막 관문이라고 할 수 있다. 하나의 차가 완성되기 위해서는 프레스-차체-도장-의장라인을 거쳐야 한다.
천장에서 내려다 본 울산3공장 의장라인 직원들은 매우 여유로워 보였다. 의자에 앉아 쉬다가도 자신의 위치로 차체가 다가오면 곧장 숙련된 솜씨로 부품을 조립했다. 뚝딱하고 부품을 조립하는 모습에서 ‘프로’의 향기가 느껴졌다.
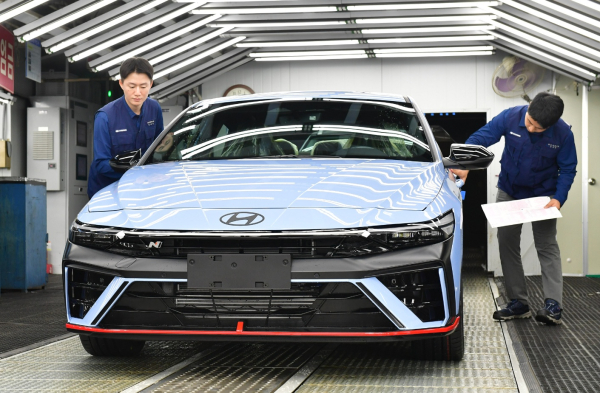
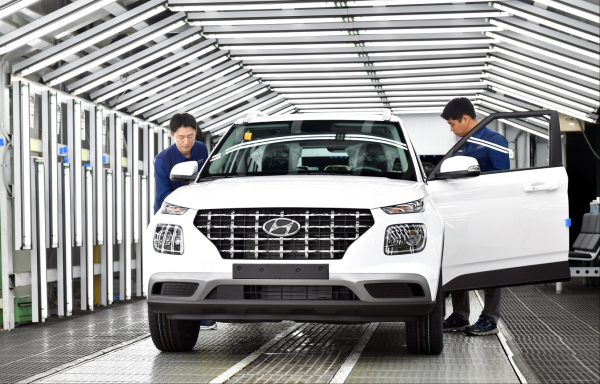
울산 3공장의 의장라인은 트림·섀시·파이널·OK테스트 등 총 4개의 라인으로 구성된다. 해당 생산라인이 하나로 연결된 것이 특징이라고 현대차 울산공장 관계자는 설명했다. 차량의 문을 탈거한 뒤에 본격적으로 부품 조립이 시작됐다. 문을 탈거하는 것은 조립 과정에서 발생할 수 있는 스크래치 등을 예방하기 위함이라고 했다.
조립의 첫 번째 단계인 트림 라인에서는 각종 전장 계열 부품(와이어링, 케이블 등)이 조립된다. 인체로 따지면 신경, 혈관이라고 볼 수 있다. 이 라인에서는 전기 신호를 전달하기 위한 배선 작업도 함께 이뤄진다. ECU(Engine Control Unit), 브레이크 부스터, 브레이크 튜브, 페달 등 차량 앞쪽에 장착되는 제동 관련 부품들도 장착된다.
두 번째 단계인 섀시 라인에서는 자동차의 구동 부품이 조립된다. 내연기관 기준으로 보면 엔진, 변속기 등이 장착되는 것이다. 전기차의 경우에는 배터리와 PE 모듈(Power Electric) 모듈이 장착된다. PE 모듈은 모터와 감속기, 인버터 등이 일체화된 것으로 내연기관의 구동 부품을 대체한다.
파이널 라인에서는 내·외부 인테리어에 해당되는 부품들이 장착되고 있었다. 시트부터 유리, 타이어 등 부품뿐 아니라 브레이크액, 냉매 액체류도 이 라인에서 주입되고 있었다. 서브 라인에서 개별적으로 조립된 도어를 재부착하며 마무리된다.
OK테스트 라인에서는 각종 품질 및 성능 테스트가 진행되고 있었다. 휠 얼라인먼트 테스트, 브레이크 테스트, 헤드램프 각도 조절, 수밀 검사, 코딩 작업 등이 진행된다고 현대차 울산공장 관계자는 설명했다.
4개의 라인에서 공통적으로 볼 수 있었던 것은 각 라인 끝에서 대기 중인 품질 검사 직원이었다. 키퍼라고 불리는 이 직원들은 각 라인 마지막 단계에서 조립 상태 등을 점검하고 있었다. 이들의 임무는 조립 과정에서 발견된 문제를 점검하고 수정하는 것이라고 한다.
하나의 차가 완성되기까지는 수 백 개의 공정을 거쳐야 한다. 해당 공정을 모두 거친 뒤 조립 불량 등을 점검하는 것은 비효율적일 수밖에 없다. 현대차가 각 라인 끝에 키퍼 역할의 직원을 배치한 이유다.
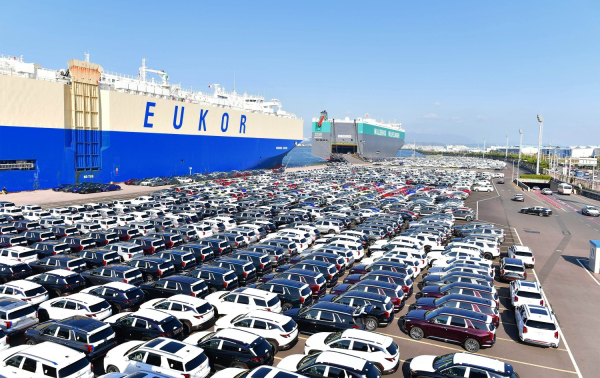
의장라인을 둘러본 뒤에는 수출선적부두로 향했다. 역시나 걸어서는 이동이 불가능했다. 그렇게 또 버스를 타고 10분 여를 달렸다. 이동 중에 재미있는 관경을 목격하기도 했다. 완성된 차들이 줄을 지어 수출선적부두로 이동하고, 그 뒤를 작은 셔틀버스가 뒤따랐다.
공장에서 생산이 완료된 차량을 운전자가 직접 수출선적부두로 이동시키고 있었다. 차량을 부두로 옮긴 운전자들은 뒤이어 도착한 셔틀에 탑승해 다시 공장으로 돌아간다. 그리고 다시 완성된 차량을 운전해 부두로 오는 작업을 반복한다.
울산공장은 5만톤(t)급 선박 3척을 동시에 접안할 수 있는 자동차 수출 전용부두를 갖췄다. 이 곳에서는 연간 최대 110만대를 전 세계 시장에 수출할 수 있다. 부두 길이는 약 830m로 4600대의 차량을 주차할 수 있다. 가장 큰 수출 선적선(7만6000t급)을 기준으로 엑센트를 최대 6900대 선적할 수 있다.
현대차 울산공장 관계자는 “매일 수 천대의 차들이 전 세계 190여 개국으로 수출된다”며 “현대차 울산공장은 수출에 강점이 있는 공장”이라고 설명했다.
ⓒ이코노미스트(https://economist.co.kr) '내일을 위한 경제뉴스 이코노미스트' 무단 전재 및 재배포 금지
많이 본 뉴스
1한국 관세 행정명령 부속서엔 25% 아닌 26%…백악관 "부속서 따라야"
2'펭리둥절' 남극에도 트럼프 관세?…"안전한 곳 없어"
3경북도, 산불피해 농어촌에 긴급자금 200억 지원
4구미시 "낙동강 따라 걷고 쉬고 즐긴다"
5울진대게, 대한민국 대표 브랜드 9년 연속 선정
6경주 벚꽃마라톤, 봄바람을 가르며 1만 5천여 명의 질주
7"수사는 안 하고 달력만 넘긴다" 홍준표 수사, 6월에는 결론날까?
8"일본산, 이젠 안녕!" 울진군, 동해안 방어 양식시대 개막
9"글로벌 인재로 미래 연다" 경북도, 3일부터 광역형 비자 시행